Our woven fabrics
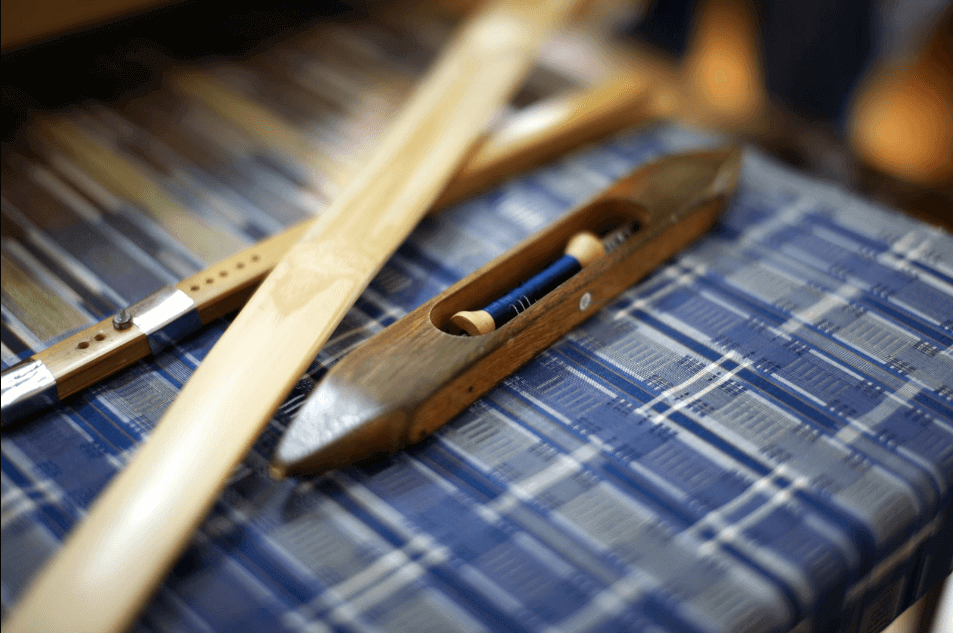
Around 1,400 warp threads are used to weave a kimono at Aya Dyeing & Weaving Studio, and more than 30 processes are involved to create each garment. All of this work is done by hand, without relying on machinery. There are reasons why we stick to this time-consuming approach, and here we introduce some of the characteristics of our weaving process.
Feature
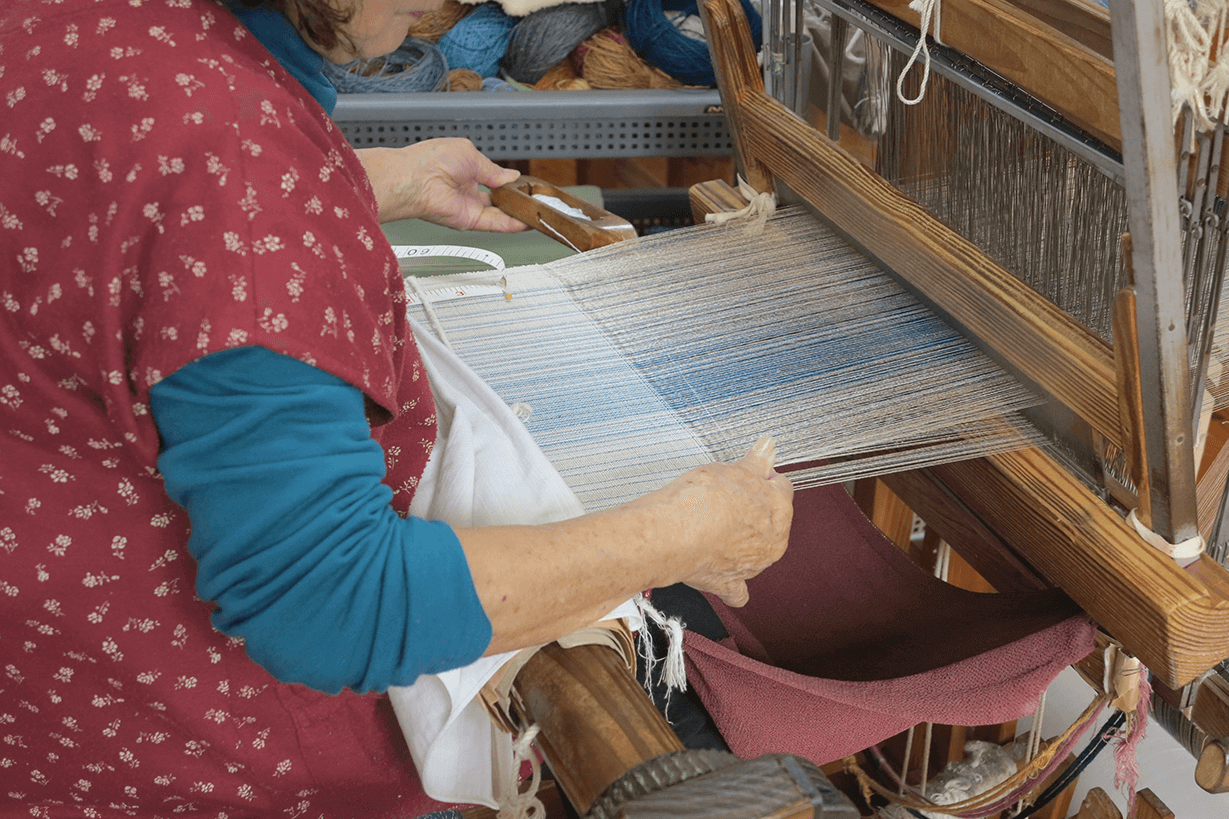
Hand-woven texture impossible from a machine weave
The charm of a handwoven fabric is above all its soft texture. Compared to machine-woven fabrics, which tend to be hard, a hand-woven kimono is soft and the obi sash is elastic and resistant to loosening or wrinkles. These are qualities that bring joy to the heart of any kimono lover. We aim to create clothing that will become more precious to the owner, the more it is worn.
In the case of machine-woven fabrics, the high speed of movement results in warp and weft threads being pulled too tight. Since the tension is much less in the case of hand-woven fabrics, the original looseness and contraction of the thread is maintained.
Traditional Ryukyu woven flower pattern
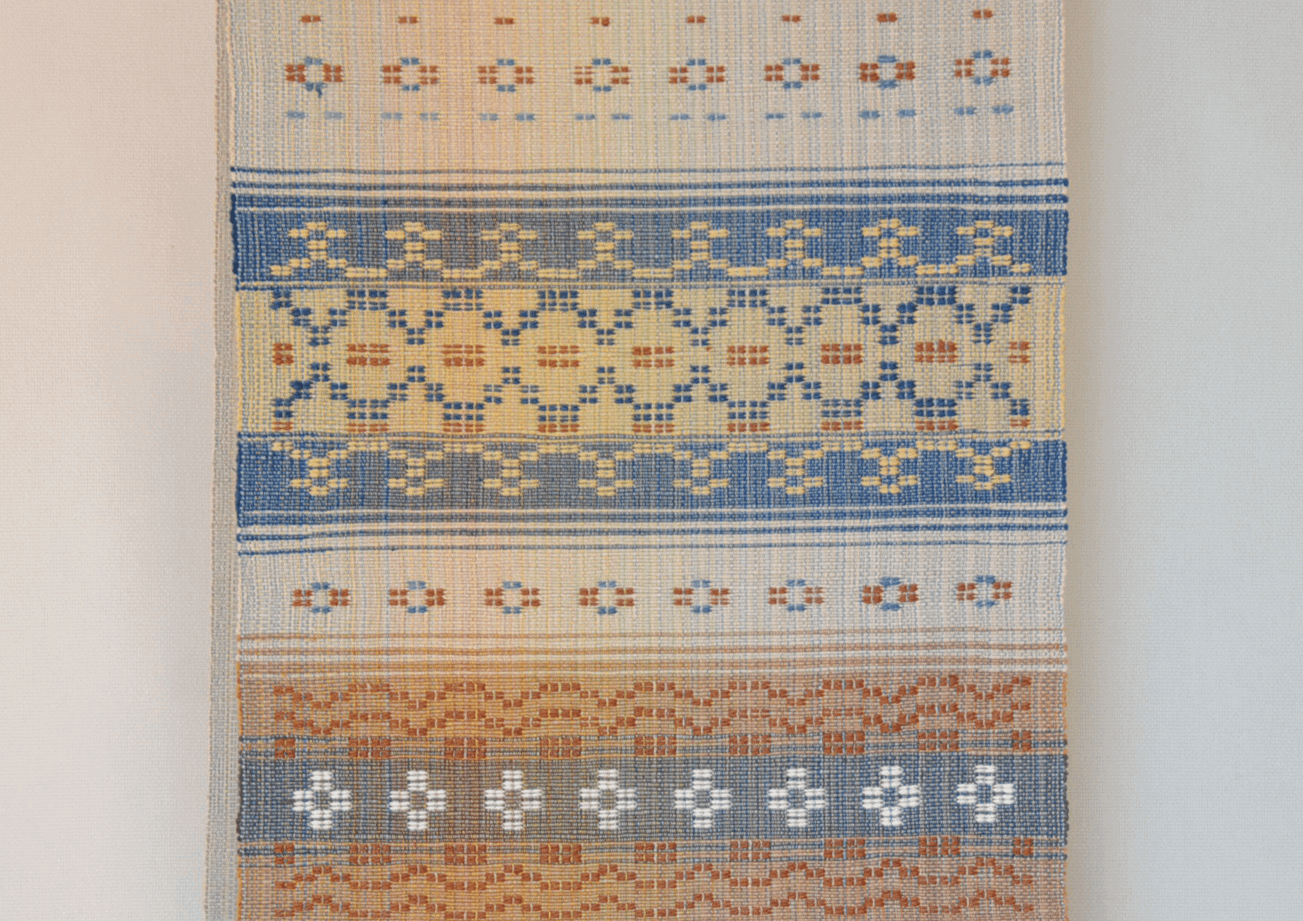
Here is an example of a traditional weaving technique in Okinawa, the birthplace of Akiyama. A variety of flower shapes appear as the result of the patterns expressed through the weaving.
Patterns and colors of sumptuous Kasuri fabrics
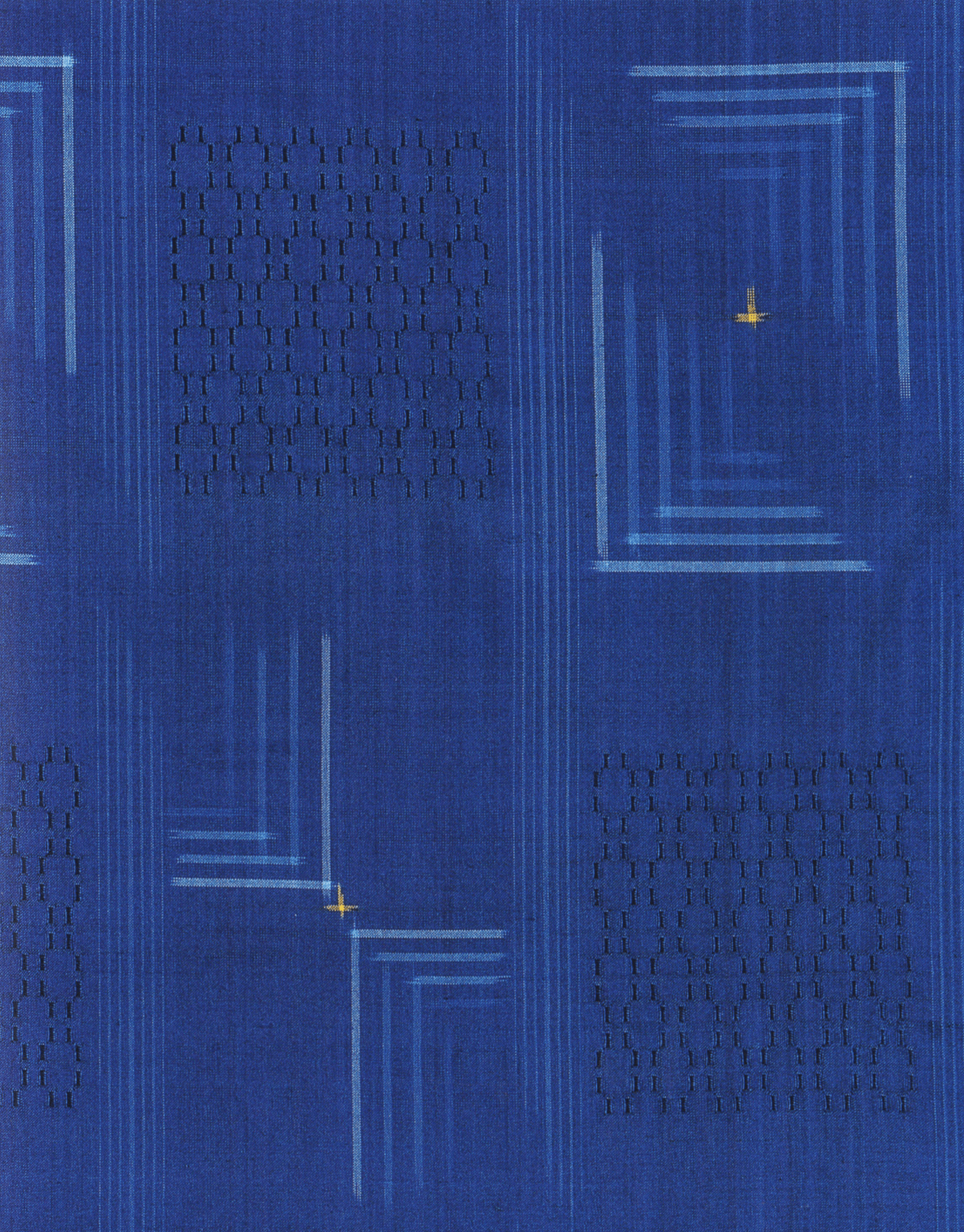
The Kasuri technique was developed to prevent threads from gathering in the weaving process, and distinctive patterns emerged as a result of this technique. Broadly speaking, the warp threads are gathered into the tategasuri while the weft threads are gathered into the yokogasuri. And when the two are combined it results in the tateyokogasuri. The bundled parts, widths, and colors can be changed depending on the sketched drawing, resulting in endless array of pattern possibilities.
Main process
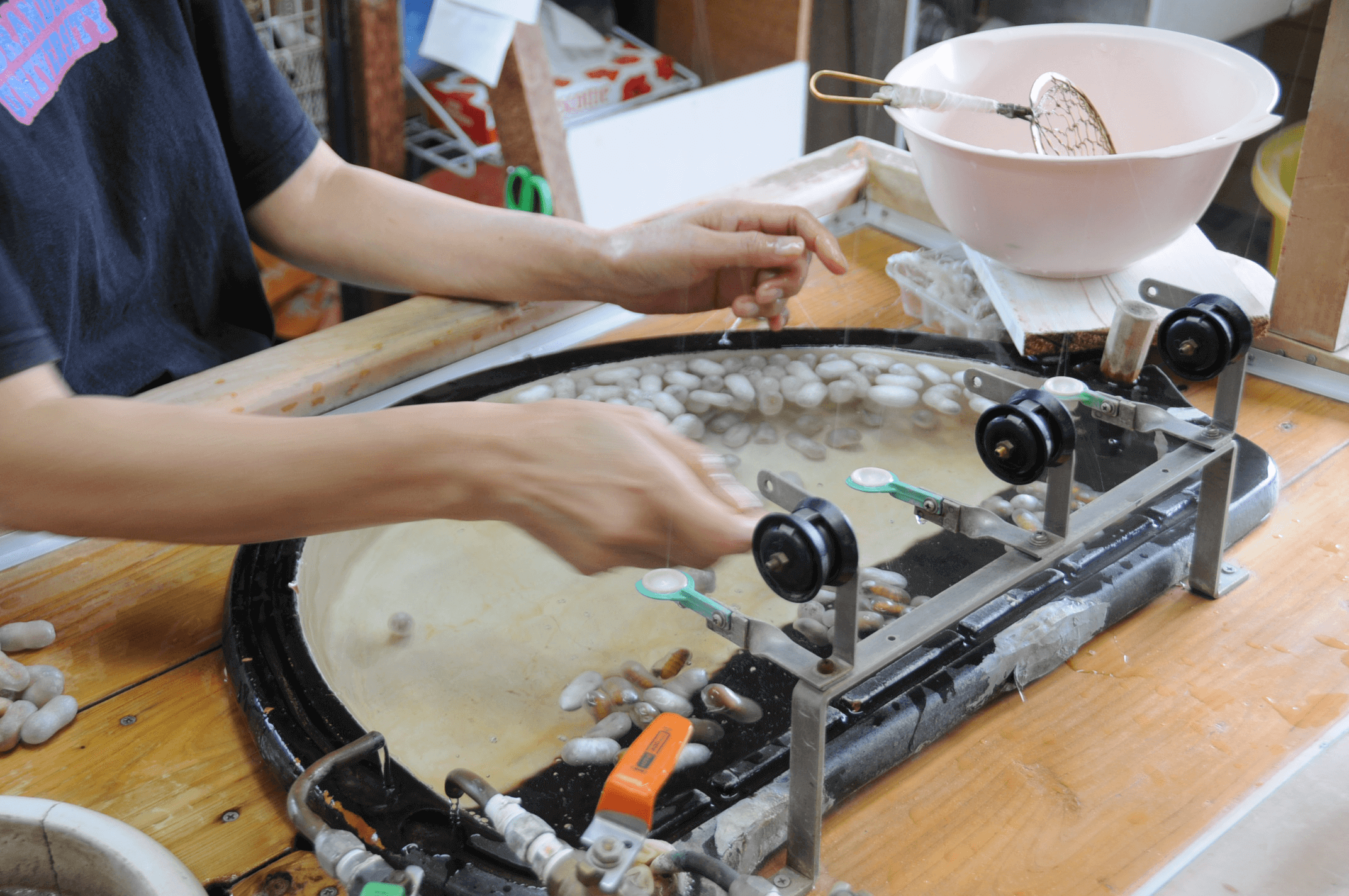
Hand-reeled silk
We make silk threads from Koishimaru cocoons. The cocoons are boiled, and then stretched to the appropriate width, while maintaining a consistent quality. This is a job that requires considerable skill and experience. Since most weft threads today are reeled automatically at high speed, the finished yarn is like an overstretched rubber band, lacking firmness and elasticity. Using such an automatic method wastes the precious silk. It is best to stick to the traditional reeling method to maintain the natural properties of the silk.
Drafting
This is the so-called “blueprint” of a fabric. The plan charts out, using the squares of graph paper, the exact arrangement and order of the warp and weft threads so that the weaver knows what to do.
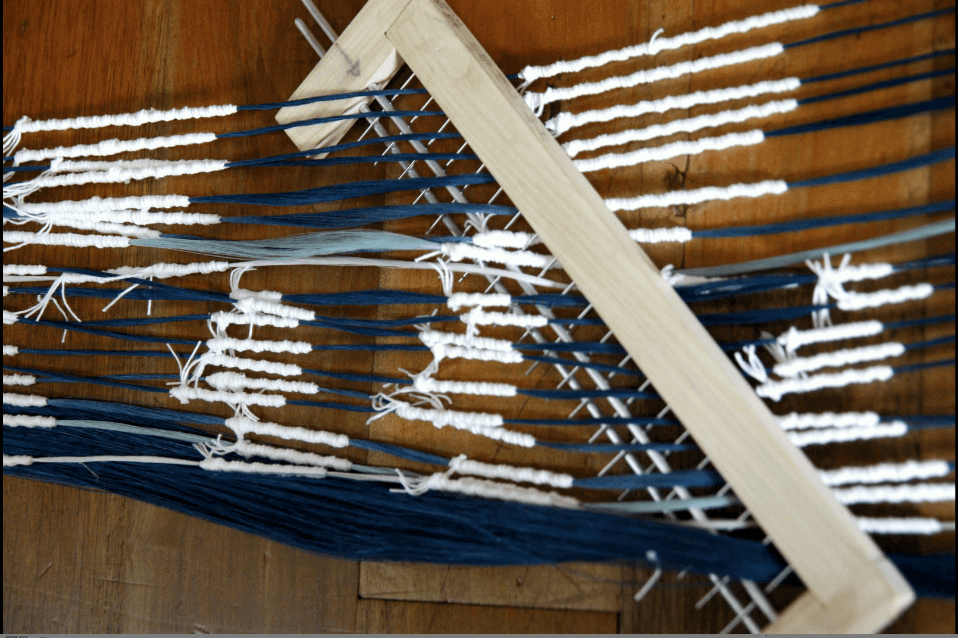
Kasuri kukuri
This is the process of binding together the yarn, according to the sketched plan. The process is simple but experience is needed to strongly, quickly, and accurately bind the thread.
Age-sage(warp threads only)
This involves shifting the Kasuri of the warp threads to create a bundle. The technique was developed for the sake of efficiency, but one can’t help feeling grateful to the people long ago who came up with such an amazing idea.
Iji(weft threads only)
Since the roots of our studio are in Okinawa, some of the terms we stem from its local dialects. One example is the term iji, which refers to the guide yarn – taneito - for the kasuri. In order to weave the weft threads, the seed yarn stretched out on the stand. And then the design for the patterns is sketched on it. Thread is bound according to the positions indicated in the plan, and those bound parts are not dyed, thus creating patterns. This is a detailed process that requires quiet concentration.
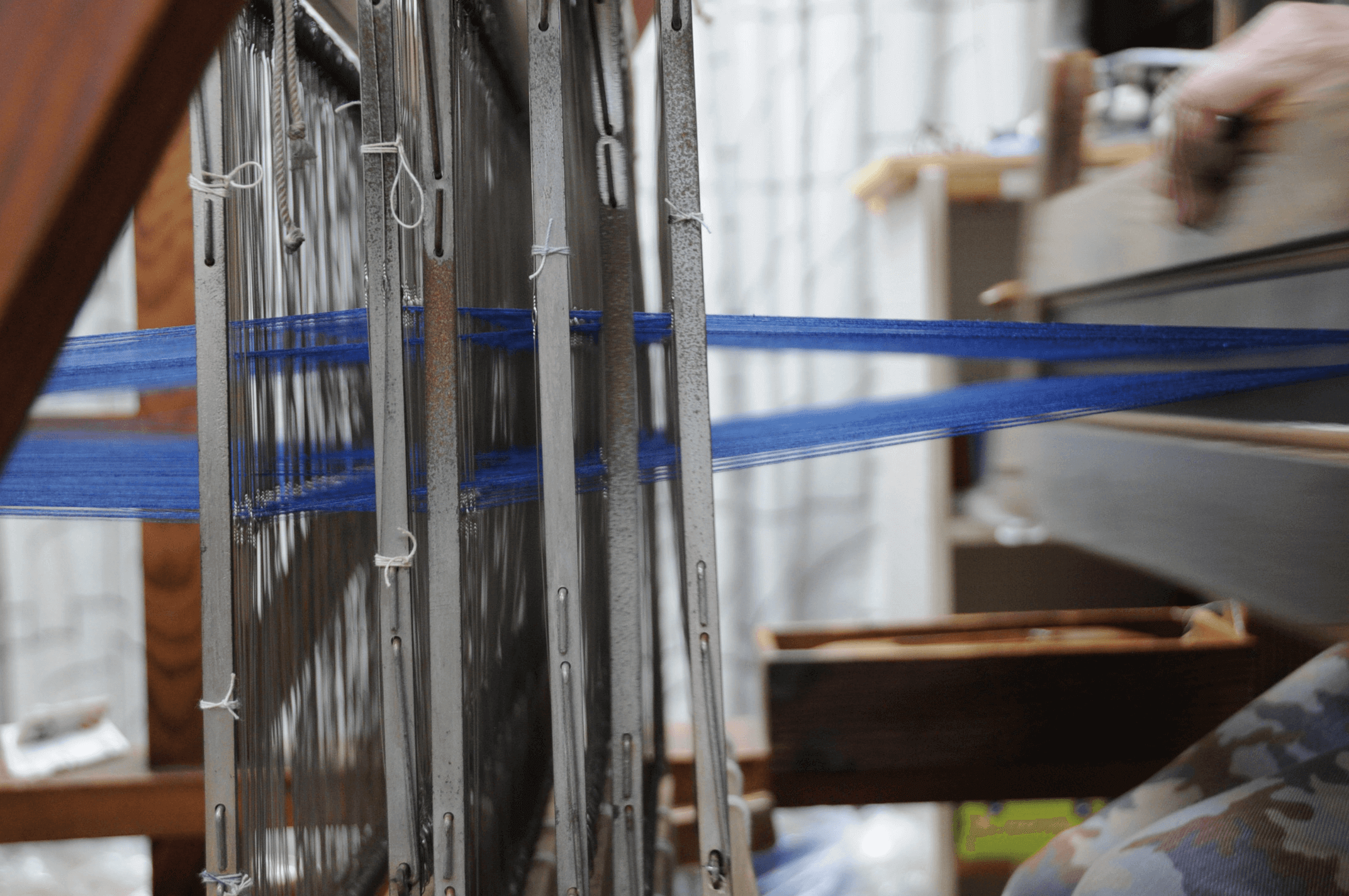
Use of the heddles (sōko) and the reed (osa)
Before the fabric is placed on the weaving machine it is passed through the heddles and reed. The 1,400 or so threads have to pass through according to the plan, without any mistakes.
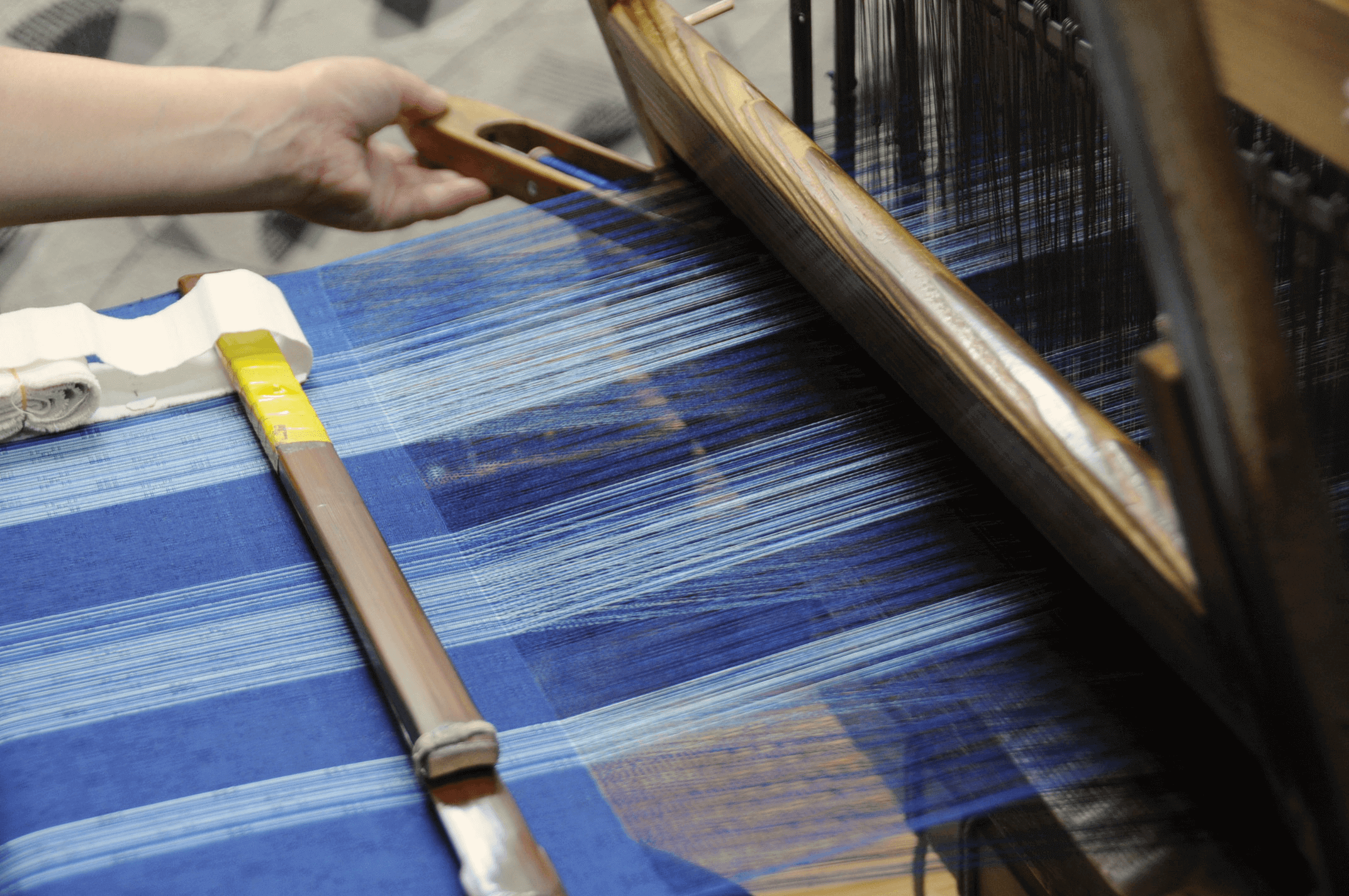
Weaving
Our studio’s weaving is based on a traditional Okinawan technique. Those traditional methods are used for the flower patterns and the Kasuri. This is the process for making the flower shapes for the production of a kimono.
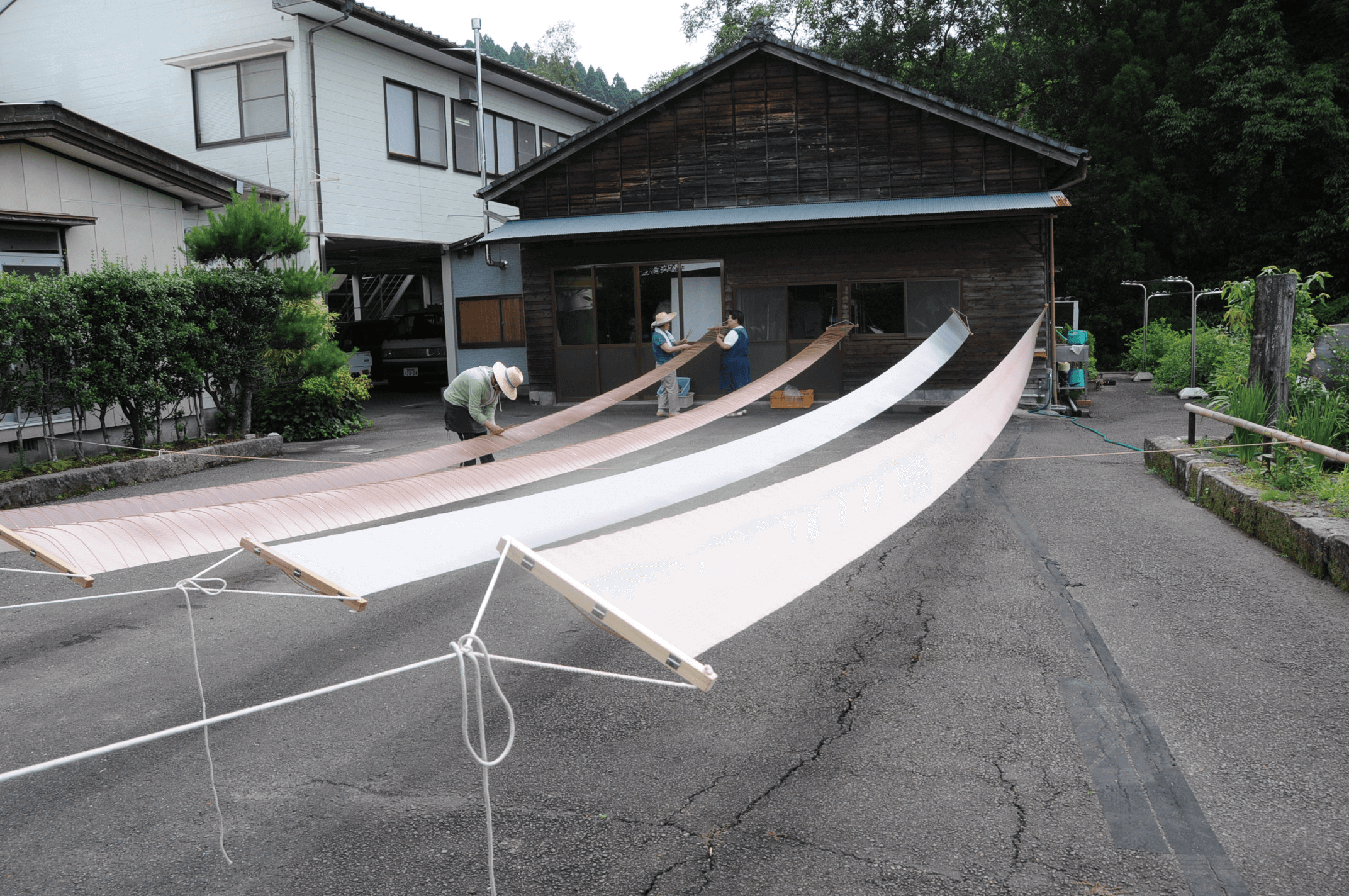
Cleaning
The fabric is passed under hot water at just the right temperature to not damage the silk in order to remove the starch. After that the width of cloth is adjusted, and the texture is finished.